VVO®
HEXPOL’s VVO (Vulcanized Vegetable Oil) products act as permanent softeners, complementary fillers, surface modifiers and thixotropic process aids. Our technical staff continually formulates new grades and uses for vulcanized oils in modern processes. Benefits:
- Improves dimensional stability (higher green strength)
- Reduces die swell
- Persistent softener (non-volatile, non-extractable, non-migratory)
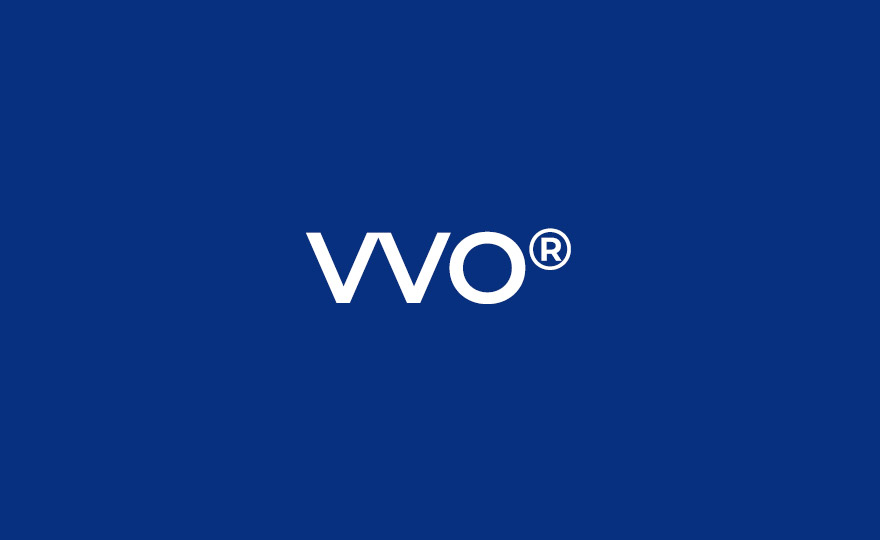
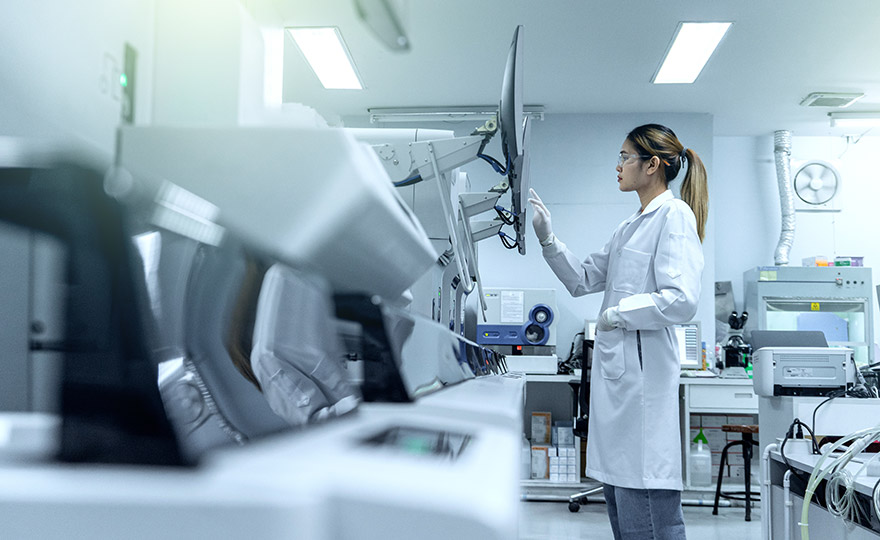
VVO Vulcanized Oils
HEXPOL Compounding is a leading North American supplier of vulcanized oils.
Our technical staff has been instrumental in formulating new grades and uses for vulcanized oils in modern processes, resulting in our extensive VVO product line.
VVO Vulcanized Oils have a number of uses:
- Permanent Softener
- Process Aid
- Filler
- Surface Modifier
Raw Materials For Performance
The physical and performance properties of today’s vulcanized oils are related to the oils, cross-linkers, modifiers and processes used to manufacture them.
The basic raw materials used for VVO products are unsaturated oils, such as soybean, rapeseed or castor oil. These naturally occurring oils are mixtures of glycerides — mostly triglycerides of mono- and polyunsaturated fatty acids. The natural properties of these oils make them suitable for cross-linking, most commonly with sulfur and sulfur monochloride, although some specialty grades are cross-linked with alternative cross-linking chemistries.
VVO oils may also be modified through the addition of plasticizers, process oils, fillers and buffers. Plasticizers and process oils are added to soften a firm grade of VVO oil. The type of plasticizer or oil used is determined by the polymer to which the VVO oil will be added. Fillers can be added to reduce production cost, enhance grinding or to partition the VVO oil. Buffers are added to reduce the acidity of the grades containing sulfur monochloride, thereby minimizing cure retardation.
Consistency Is Key
Modern rubber products and processes require the use of consistent raw materials. Vulcanized oils are no exception. Time, temperature, post-cure and agitation are only some of the process conditions that must be controlled to produce a consistent vulcanized oil product. HEXPOL’s modern production controls ensure consistent quality and performance of its VVO vulcanized oils. Your process and final product properties will determine the type of VVO oil that is right for you. VVO oils can be used in numerous applications, including:
- Roll products
- Molded products
- Extruded products
- Sponge products
VVO® Vulcanized Oil Is A Complementary Filler
At higher loadings, VVO vulcanized oil behaves like a filler without creating hardness or “boardiness” in a compound. In addition, it improves properties like dimensional stability and green strength. It will reduce tack without affecting the cured knitting of the compound. Its consistency does not change with temperature so it can provide structure to an extruded strip or sponge compound. This lends support before and during cure.
VVO® Vulcanized Oil is a Permanent Softener
As a partial replacement for plasticizer or oil in a compound, VVO vulcanized oil is:
- Non-blooming
- Non-volatile
- Non-migrating
- Non-extractable
It will help maintain compound durometer and flexibility over time, even in difficult service conditions like flexographic or roll applications. In general, two parts VVO oil can be substituted for one part plasticizer or oil, up to 15 parts, with little effect on other compound properties.
VVO ® Vulcanized Oil Is A Process Aid
VVO vulcanized oil creates a unique thixotropic rheology in a compound. This allows it to flow freely under mechanical pressure but return to a static state when the stress is removed. This quality allows for:
- Lower temperature build-up during mixing
- Wider temperature range for optimum calendering
- Reduced shrinkage
- Reduced cold flow
- Increased green strength
- Improved mold fill
- Reduced die swell
VVO® Vulcanized Oil Is a Surface Modifier
VVO vulcanized oil in a compound reduces abrasion resistance. This allows better polishing or grinding of roll compounds. Pencil erasers are loaded with VVO oil because of its ability to reduce abrasion resistance. As the surface of the eraser wears away, a new, clean surface is uncovered to wipe away the graphite contained in the pencil. VVO oil imparts a supple and velvety feel to compounds before and after curing. Besides facilitating mold removal, VVO oil improves surface appearance.
VVO® Vulcanized Oil Products
- VVO® Vulcanized Oils
- VVO® Applications
- VVO® Vulcanized Oil Products for Extruded Processes
- Neophax® A
- 219 White
- 2-L Brown
Benefits of VVO® Vulcanized oil:
- Provides dimensional stability
- Increases green strength
- Absorbs oil
- Smooths surface
- Non-extractable plasticizer
VVO® vulcanized oil products for molded processes
- Carbelex 20
- 2-L Brown
Benefits of VVO® Vulcanized oil:
- Aids process/mold flow
- Increases green strength
- Smooths finish
- Serves as a non-extractable plasticizer
- Reduces mold fouling
VVO® Vulcanized Oil Products for Roll Processes:
- 2-L Brown
- Neophax® A
Benefits of VVO® Vulcanized oil:
- Non-extractable plasticizer
- Resists oil and solvents
- Reduces migration
- Acts as a softener
- Aids processing in soft compounds
- Controls durometer
- Aids finishing/grinding
VVO® Vulcanized Oil Products for Sponge Processes:
- Neophax® A
- 74 Brown
Benefits of VVO® Vulcanized oil:
- Non-extractable plasticizer
- Extends oils
- Reduces migration
- Absorbs oil in very soft compounds
- Modifies compression set
- Acts as a softener